
La productividad de una planta industrial está directamente ligada al correcto funcionamiento de las máquinas. Obviamente, si una línea se para por un fallo de una de sus máquinas, la productividad disminuirá. Un análisis detallado de la instalación permite la medida de la importancia relativa de cada uno de los factores que pueden provocar averías, y la puesta en marcha de un plan de eliminación de los mismos, para mantener equipos e instalaciones a un nivel óptimo. A partir de este instante se establece cuál es el mantenimiento productivo que se debe aplicar, formando a los operarios de la línea para garantizar la continuidad del sistema.
Existen diferentes tipos de mantenimientos que se pueden aplicar en un entorno industrial y que repercuten en la disposición de una maquinaria en buen estado. A continuación se describen estos tipos de mantenimiento.
Mantenimiento planificado.
El mantenimiento rutinario y periódico, basado en valoraciones correctas de las condiciones del equipo, debe ser planificado en función de las prioridades y los recursos actuales y futuros. El mantenimiento planificado eficiente y efectivo en cuanto al coste, requiere la estrecha colaboración de todos los departamentos implicados. Las actividades de mantenimiento planificado las realizan técnicos especialistas y están orientadas a corregir, prevenir y predecir averías. Dichas actividades necesitan datos de la eficiencia de los equipos, estadísticas de averías e información de los operarios y directores de producción.
La documentación de los resultados de mantenimiento constituye un elemento acreditativo de la calidad de éste. Los informes de mantenimiento registran las reparaciones y servicios realizados para restablecer las condiciones de funcionamiento normales del equipo. En estos informes, el personal de mantenimiento, registra las reparaciones de averías y los trabajos especificados en la planificación establecida.
Mantenimiento preventivo.
La finalidad del mantenimiento preventivo es la reducción del número de paradas derivadas de averías imprevistas. En su planteamiento tradicional, el mantenimiento preventivo se basa en paradas programadas para realizar una inspección detallada y para sustituir las piezas desgastadas.
Mantenimiento predictivo.
El mantenimiento predictivo consiste en la detección y diagnóstico de averías antes de que éstas se produzcan, con el fin de programar paradas para reparaciones en los momentos oportunos. En otras palabras, sirve para diagnosticar las condiciones del equipo cuando está en marcha y determinar cuándo requiere mantenimiento, basándose en que normalmente las averías no se producen de golpe, sino que suelen avisar mediante una cierta evolución. Los objetivos principales del mantenimiento predictivo son:
- Reducir averías y accidentes que causan los equipos.
- Reducir los tiempos y costes de mantenimiento.
- Incrementar los tiempos operativos y la producción.
- Mejorar la calidad de los productos y servicios.
Cuando las reparaciones pueden ser caras o las averías ocasionan pérdidas importantes las empresas pasan del mantenimiento periódico al predictivo. La tecnología de diagnóstico de máquinas mide la fatiga del equipo, su deterioro, la resistencia, el rendimiento y otras propiedades, sin tener que recurrir al desmantelamiento.
El Mantenimiento Productivo Total TPM.
El Mantenimiento Productivo Total TPM (Total Productive Maintenance) es un conjunto de técnicas orientadas a eliminar las averías a través de la participación y motivación de todos los empleados. La idea fundamental es que la mejora y buena conservación de los activos productivos es una tarea de todos, desde los directivos hasta los ayudantes de los operarios. Para ello, el TPM se propone cuatro objetivos:
- Maximizar la eficacia del equipo.
- Desarrollar un sistema de mantenimiento productivo para toda la vida útil del equipo que se inicie en el mismo momento de diseño de la máquina (diseño libre de mantenimiento) y que incluirá a lo largo de toda su vida acciones de mantenimiento preventivo sistematizado y mejora de la mantenibilidad mediante reparaciones o modificaciones.
- Implicar a todos los departamentos que planifican, diseñan, utilizan o mantienen los equipos.
- Implicar activamente a todos los empleados, desde la alta dirección hasta los operarios, incluyendo mantenimiento autónomo de empleados y actividades en pequeños grupos.
La eficacia de los equipos se maximiza por medio del esfuerzo realizado en el conjunto de la empresa para eliminar las “seis grandes pedidas” que restan eficacia a los equipos. Una consecuencia importante de la implantación del TPM en la fábrica es que los operarios toman conciencia de la necesidad de responsabilizarse del mantenimiento básico de sus equipos con el fin de conservarlos en buen estado de funcionamiento y, además, realizan un control permanente sobre dichos equipos para detectar anomalías antes de que causen averías. El TPM incluye como primeras actividades la limpieza, la lubricación y la inspección visual.
El TPM promueve la concienciación sobre el equipo y el automantenimiento por lo que es necesario asegurar que los operarios adquieren habilidades para descubrir anomalías, tratarlas y establecer las condiciones óptimas del equipo de forma permanente.En estas condiciones, la implantación TPM requiere una metodología adecuada a las características de la empresa y sobre todo, formación de las personas. De una forma esquemática, el proceso de implantación TPM se puede desplegar en las siguientes fases:
Fase preliminar.
En una fase preliminar es necesario modelizar la información relacionada con mantenimiento, identificando y codificando equipos, averías y tareas preventivas.
Fase 1.- Volver a situar la línea en su estado inicial
El objetivo debe ser dejar la línea en las condiciones en las que fue entregada por parte del proveedor el día de su puesta en marcha: limpia, sin manchas de aceite, grasa, polvo, libre de residuos, etc.
Paso 2.- Eliminar las fuentes de suciedad y las zonas de difícil acceso
Una fuente de suciedad (fugas de aire o de aceite, caídas de componentes, virutas de metal, etc.) es aquel lugar en el que, aunque se limpie continuamente, sigue generando suciedad. Estas fuentes de suciedad hay que considerarlas como causas de un mal funcionamiento o anormalidades de los equipos, aunque está claro que unas repercutirán más que otras en el rendimiento de las instalaciones.
Paso 3.- Aprender a inspeccionar el equipo
Para el proceso de implantación del TPM es fundamental que el personal de producción, poco a poco, se vaya encargando de más tareas propias de mantenimiento, hasta llegar a trabajar de forma casi autónoma. Para ello es imprescindible formación para transmitir los conocimientos necesarios a los operarios de la línea sobre el funcionamiento de las máquinas y los equipos. Esta formación cada vez será más detallada y abarcará más tareas multidisciplinares.
Paso 4.- Mejora continua
En este paso los operarios de producción realizan las tareas de TPM de forma autónoma, se hacen cargo de las técnicas necesarias y proponen mejoras en las máquinas que afecten a nuevos diseños de línea. Los responsables verifican los esfuerzos para mejorar los procedimientos de mantenimiento preventivo y supervisan sus actividades orientadas a elevar la rentabilidad económica de la planta. En esta fase cobra vital importancia la determinación de las causas de averías para la cual se pueden utilizar las mismas técnicas de calidad total que se usan en SMED.
Una vez iniciado un programa TPM, la calidad de su proceso de implantación debe ser auditada por el departamento de mantenimiento de cara a controlar los costes, comprobar que las actividades planificadas se han realizado y plantear objetivos para siguientes fases.
Los 8 pilares del TPM.
Mejoras enfocadas. Grupos de trabajo interdisciplinares formados en técnicas para la mejora continua y la resolución de problemas. Estos grupos enfocarán su trabajo a la eliminación de las pérdidas y la mejora de la eficiencia.
Mantenimiento planificado, actividades de mantenimiento preventivo, predictivo y correctivo orientadas a la prevención y eliminación de averías.
Mantenimiento autónomo, basado en operaciones de inspección y pequeñas actuaciones sencillas, realizadas por los operarios de las máquinas.
Mantenimiento de calidad, basado en actuaciones preventivas sobre las piezas de las máquinas que tienen una alta influencia en la calidad del producto.
Prevención de mantenimiento, basado en la gestión temprana de las condiciones que deben reunir los equipos o las instalaciones, para facilitar su mantenibilidad en su etapa de uso.
Mantenimiento áreas soporte, buscando el apoyo necesario para que las actividades de TPM, aseguren la eficiencia y la implicación global.
Mejora de la polivalencia y habilidades de operación. Formación continua del personal de producción y mantenimiento para mejorar sus habilidades y aumentar su polivalencia y especialización.
Seguridad y entorno, la seguridad y prevención de efectos adversos sobre el entorno son temas importantes en las industrias responsables. La seguridad se promueve sistemáticamente en las actividades de TPM.
Índice de Eficiencia Global del Equipo.
En este punto conviene definir un sistema de indicadores accesible y fiable para capturar, medir, analizar y evaluar los resultados y desviaciones respecto al objetivo de manera metódica y fiable. Indicadores como el rendimiento de la mano de obra, las horas dedicadas a trabajos urgentes, los costes de reparación o la disponibilidad son válidos para estos sistemas aunque en el entorno Lean cobra vital importancia el indicador numérico natural para el TPM, denominado Índice de Eficiencia Global del Equipo, conocido como OEE (Overall Equipment Efficiency).
OEE es un indicador que se calcula diariamente para un equipo o grupos de máquinas y establece la comparación entre el número de piezas que podrían haberse producido, si todo hubiera ido perfectamente, y las unidades sin defectos que realmente se han producido. Para la utilización de este indicador, se utilizan los índices de Disponibilidad, Eficiencia y Calidad. OEE es el producto de estos tres índices, de manera que:
OEE (Eficiencia Global de Equipos Productivos) = D x E x C
El coeficiente de disponibilidad (D) es la fracción de tiempo que el equipo está operando realmente reflejando las pérdidas por averías y paradas. Para su cálculo se parte del tiempo disponible, también llamado tiempo de carga, que es el tiempo total de operación menos el tiempo muerto, planificado o necesario, tal como la interrupción del programa de producción, tiempos de descanso y reuniones diarias de taller. El tiempo operativo es el tiempo de carga menos el tiempo que la máquina está parada debido a averías, preparaciones, ajustes, cambio de técnicas y otras paradas. El coeficiente de eficiencia (E) mide el nivel de funcionamiento del equipo contemplando las perdidas por tiempos muertos, paradas menores y perdidas por una velocidad operativa más baja que la de diseño.
Por último, el coeficiente de calidad (C) mide la fracción de la producción obtenida que cumple los estándares de calidad reflejando aquella parte del tiempo empleada en la producción de piezas defectuosas o con errores.
Disponer de un OEE de, por ejemplo, 60% significa que de cada 100 piezas buenas que la máquina podría haber fabricado, sólo ha producido 60. Este tipo de cálculo hace que el OEE se convierta en un examen severo. Por ejemplo, si los tres índices son del 90%, el OEE será 72,9%. En general, se considera que un muy buen OEE se situaría por encima del 85%. En la práctica, se acepta el establecimiento de objetivos distintos para cada índice, y así, por ejemplo, se podría plantear una disponibilidad del 90%, una eficiencia del 95% y un índice de calidad del 99,9%, lo que representa un OEE del 85%.
El cálculo del OEE es interesante porque en un único indicador se evalúan todos los parámetros fundamentales de la producción industrial y constituye una de las claves del Lean. De acuerdo con lo expuesto, la mejora de la eficacia con la que trabajan los equipos y las instalaciones permite el incremento de la eficiencia de todo el sistema productivo. El valor numérico de la eficiencia global es un porcentaje que se determina con anterioridad a la introducción de mejoras para conocer el punto de partida del equipo cuya eficiencia se quiere incrementar. Este indicador permite valorar la progresión Lean a medida que se van introduciendo sucesivas mejoras. La importancia del indicador es tal que muchas consultoras/implantadoras Lean desarrollan toda su metodología alrededor de la explotación del OEE.
Ejemplo de cálculo del OEE:
- Si tenemos un turno de 8 horas, y hay 30 minutos de comida y dos recesos de 15 minutos, Entonces el tiempo real de producción es de 7 hrs efectivas.
- Si de esas 7 hrs efectivas, se pierde 1 hora en tiempos muertos (entre preparaciones y problemas de producción).
- Suponiendo que se deberían sacar 1000 piezas y solo se producen 920, y hay 30 de retrabajos (los retrabajos SIEMPRE se consideran desperdicio para el OEE), entonces tenemos:
DISPONIBILIDAD = 6 hrs reales / 7 hrs teoricas = 86% .
DESEMPEÑO = 920 Piezas reales / 1000 piezas teoricas = 92% .
CALIDAD = 30 retrabajos / 920 piezas totales = 96%.
OEE = 86% x 92% x 96% = 76%
Un OEE de clase mundial se considera, en terminos generales, de 85%. En la mayoría de los países, el OEE ronda el 60%. Una iniciativa de OEE dará siempre buenos frutos, sin embargo, para lograr resultados constantes y rápidos, se debe de leer el OEE en tiempo real.
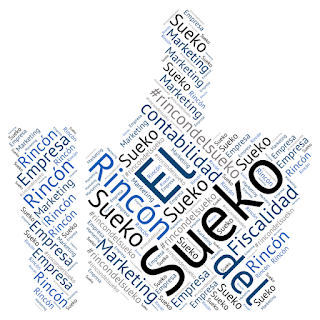
#rincondelsueko en Twitter, Facebook, Flipboard y Google+
No hay comentarios:
Publicar un comentario