
Cuando una empresa decide implantar un sistema Lean debe apostar firmemente por la formación de sus recursos humanos. Esta formación puede realizarse a través de los siguientes pasos:
- Valoración del capital humano. Evaluación de los niveles de conocimientos y habilidades actuales del equipo de trabajo.
- Determinación de los conocimientos, habilidades y recursos requeridos perseguidos.
- Programación temporal y de contenidos de la formación, fijando una agenda detallada de formación, tanto a nivel individual como en grupo.
- Evaluación de la efectividad de la formación.
Para el primer paso pueden utilizarse sistemas de valoración del capital humano específicamente diseñados para entornos Lean. Estos sistemas parten de una base de datos en la que incluyen las habilidades de cada uno de los trabajadores. Dichas habilidades las agrupan en tres categorías: técnicas (conocimientos básicos, matemáticas, medidas, etc.), humanas (cualidades personales, habilidades sociales, etc.) y Lean (conocimientos sobre técnicas, mejoras..).
Una vez que se conocen dichas habilidades de la plantilla, se establecen los planes de formación más adecuados, se asigna al trabajador al puesto más idóneo y se establece un sistema de recompensas y premios. Sin embargo, estos sistemas solo se aplican en grandes empresas con departamentos de recursos humanos potentes y estructurados.
Actualmente ya existen empresas especializadas en la formación en técnicas Lean. En la mayoría de los casos son pequeñas empresas creadas por profesionales provenientes de departamentos de implantación Lean de grandes empresas o bien empresas de consultoría que compaginan sus servicios con la formación, lo que les permite transmitir sus experiencias prácticas y casos de éxito. El plan de formación puede instrumentalizarse a partir de varias acciones simultáneas entre las que pueden aconsejarse:
- Visitas de fábricas que hayan implantado con éxito métodos Lean en el marco de una estrategia de benchmarking.
- Organización de seminarios o cursos específicos sobre conceptos y técnicas Lean.
En este caso, es muy conveniente que incluyan la participación de docentes con experiencias reales en implantación, discutiendo la forma de su posible aplicación interna en la empresa. Apoyarse en la gran cantidad de información escrita y/o audiovisual existente combinada con formación a distancia y discusiones en grupo.
En cualquier caso, estas acciones deben ir seguidas de aplicaciones reales prácticas, preferiblemente a partir de un proyecto piloto en un área acotada y, si tiene éxito, utilizarlo como demostración. En una primera etapa se deben formar las personas que han de participar en la implantación lean con el objetivo de motivarlas y que adquieran una fuerte confianza en el sistema que transmitirán al resto del personal. Los principales objetivos a tratar en esta formación preliminar deben ser:
- Aprender los aspectos clave y principios del sistema, especialmente la mejora continua.
- Aprender a analizar las operaciones y su flujo, detectando despilfarros.
- Aprender a representar el proceso y su flujo por medio del mapa de flujo de valor (VSM).
- Asumir el proceso de mejora continua como herramienta clave para la mejora de la competitividad.
A partir de esta etapa de inicio ya se pueden establecer planes concretos de formación en las distintas técnicas. Una lista sintetizada de los aspectos que debería comprender una formación Lean son:
- La metodología de las 5S y los pasos detallados para su implantación.
- Los fundamentos de la garantía de la calidad total a partir de las técnicas Lean: jidoka, andon, mecanismos anti-error y la matriz de autocalidad.
- Los principios de las técnicas SMED para la reducción de los tiempos de preparación.
- Los principios del TPM para la implantación de un mantenimiento preventivo que ara minimice los tiempos de parada por avería.
- La utilidad de los sistemas de indicadores para la medida de la eficiencia del sistema productivo.
- Las técnicas prácticas par análisis de causas de defectos y errores: los cinco ¿por qué?, 5W+1H, la clasificación ABC de Pareto, las cuatro M o el diagrama de Ishikawa.
- Las ventajas del sistema pull a partir de un flujo sincronizado, continúo en pequeños lotes, mediante la utilización del sistema kanban.
- Los conceptos relativos al nivelado de la producción para su adaptación a la demanda, Heijunka.
- Los mecanismos del sistema JIT proveedor/cliente.
Al final de este periodo formativo, dependiendo de cada área y función y del plan de implantación Lean planificado, la empresa debería contar con personal líder capacitado para:
- Diagnosticar el estado de un sistema productivo y establecer indicadores para evaluar el proceso de mejora continua.
- Promover, implantar y gestionar con éxito un programa de mejora continua basado en la eliminación de despilfarros.
- Crear e implantar sistemas de control del proceso para reducir o eliminar completamente los defectos.
- Concienciar a los operarios de la enorme importancia de su participación activa en los programas de propuestas para la mejora de los procesos.
- Planificar y organizar la implantación real de las técnicas básicas del Lean: 5S, SMED, TPM, Jidoka,
Si las características del sistema productivo (productos-procesos) lo aconsejasen, la formación también debería orientarse a disponer de personal capaz de:
- Organizar e implantar un sistema pull de producción para fabricar sólo lo que se necesita, en el tiempo en que se necesita, con la calidad especificada y al mínimo coste.
- Diseñar células “U” para favorecer el hecho de disponer sólo del material necesario para producir y estudiar el aprovisionamiento de la línea.
- Aplicar sistemas de nivelado de la producción y reducir las pérdidas por falta de balanceo.
- Desplegar un sistema de gestión JIT de proveedores y clientes.
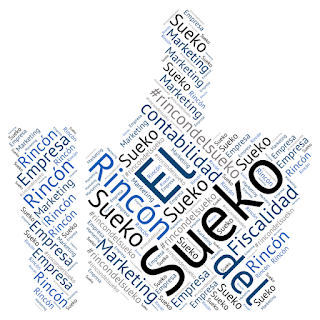
#rincondelsueko en Twitter, Facebook, Flipboard y Google+
No hay comentarios:
Publicar un comentario