
Aplicación de Lean Manufacturing.
La aplicación de Lean Manufacturing es un tema que no se encuentra normalizado y no existe una única forma de aplicar las herramientas de Lean. Cada empresa posee sus propias características culturales dentro de las cuales se encuentran su personal, recursos, maquinarias, espacios físicos, desarrollo gerencial, visión, misión, etc. lo cual las hace únicas e inimitables. El objetivo de la transformación del proceso a los principios lean es conseguir:
- Eliminar de los procesos las actividades que no aporten valor añadido (desperdicios en forma de producción excesiva, stocks, etc.).
- Introducir la flexibilidad necesaria para adaptar la producción a una demanda fluctuante.
Para su aplicación práctica se propone los siguientes pasos:
Fase 1. Formación:
Se basa, en realizar seminarios destinados al equipo humano de la empresa involucrado en la transformación del sistema productivo. Se incidirá especialmente en los conceptos, métricas y herramientas del Lean Manufacturing. Más adelante le dedicaremos un post.
Fase 2. Recogida de datos:
Se basa, en realizar registros actuales de los distintos procesos operacionales involucrados en el sistema productivo.
- Ritmo de trabajo. Análisis del tiempo real disponible en los almacenes, ajustado a distintas situaciones de demanda de los clientes en tipo de producto y volúmenes de producción y obtención de los correspondientes ritmos idóneos de trabajo.
- Toma de datos de las operaciones. Este punto es de especial importancia, dado que el éxito de la implementación dependerá, en gran medida, de la fiabilidad de estos datos. Los datos se referirán a operaciones, equipamientos productivos, tiempos, flujos y recursos utilizados.
Fase 3. Análisis de los datos:
En esta fase se analizan los datos recopilados:
- Análisis de las operaciones. Basado en la determinación de las operaciones de los procesos para los distintos componentes de los productos. Se incluirán todos los aspectos operativos, de calidad, de mantenimiento y de recursos humanos.
- Diagrama de precedencias. Se identificarán exigencias de secuenciación de operaciones en los procesos, obteniendo las secuencias posibles y las atribuciones de valor de las operaciones.
- Diagrama de flujo. Incluirá las secuencias de operaciones de productos y componentes, agrupados por familias en un flujo que ha de conducir al cliente de la forma más regular y constante posible.
- Mapa de la cadena de valor. Cuyo objetivo es crear una fuente de información global, visualizada a través del flujo de producto, materiales e información.
- Identificación de los desperdicios. Como conclusión del análisis de los datos y las operaciones y apoyándose en el mapa de la cadena de valor, se identificarán los focos de desperdicio en las actividades de los procesos y un plan para su eliminación o minimización. Ello permitirá asimismo, establecer las prioridades en la mejora continua.
Fase 4. Fase de estudio:
- Análisis del nivel de calidad asegurada tras la eliminación de los desperdicios. Se desarrolla un plan para el aseguramiento de la calidad en los procesos.
- Análisis de la disponibilidad, fiabilidad y eficiencia de los equipos productivos. Se desarrolla un plan para garantizar el correcto funcionamiento y mejora el tiempo de parada.
- Definición y diseño de la distribución en planta (layout). Se efectuará constituyendo tres niveles: layout general, layout de cada proceso y layout de cada operación de cada proceso. Se determinarán las posiciones de las estaciones de trabajo, la posición de trabajo de los operarios y el recorrido de materiales y personas.
- Descripción de las tareas por puesto de trabajo. Con la asignación de las tareas a cada trabajador y la determinación de las actividades con valor añadido y sin él, las esperas y los desplazamientos.
- Balanceo de operaciones. Basado en el análisis de las capacidades de operación para cada etapa de cada proceso. Se tratará de ajustar la capacidad productiva a la demanda, determinando los recursos necesarios. Se priorizará la mejora en los cuellos de botella y en operaciones con más desperdicios.
- Balance de puestos de trabajo. Basado en el análisis de la capacidad de cada puesto, de acuerdo con las tareas asignadas, tratándose de ajustar los recursos necesarios para que pueda operar. Se priorizará la mejora de los puestos con tareas que incluyan más esperas, desplazamientos y desperdicios en general.
Fase 5. Fase de evaluación de los resultados esperados:
- Definición de las condiciones de trabajo. Determinación de las opciones de desarrollo de los procesos para distintos niveles de producción, de acuerdo con la cantidad de trabajadores, los lotes de producción, transportes, materiales en proceso, tiempo de proceso total o lead time, espacio ocupado y, desde luego, productividad. Es indispensable que se den las condiciones que aseguren el flujo regular y los tiempos (calidad, mantenimiento y formación del personal).
- Flujos de materiales, trabajadores, elementos de transporte e información. Determinación gráfica de las distintas soluciones a través de los correspondientes flujos, con aplicación de soluciones visuales tales como: etiquetas kanban, contenedores de los procesos, señalización visual de etapas y proceso en planta. Se asignarán espacios para stock, almacenes, entradas y salidas de material y rutas de reaprovisionamiento. Se definirán, asimismo, las cantidades y capacidades de los medios de transporte de materiales y productos; y los tiempos de materiales detenidos.
Fase 6. Fase de optimización:
En la medida de lo necesario, en esta etapa se optimizará el diseño global de la planta, su implantación y el desarrollo de la producción, por medio de un simulador informático estándar. La simulación de procesos permitirá un análisis técnico de la globalidad del conjunto de procesos de la planta. Como resultado se obtendrán los valores optimizados de los parámetros del sistema productivo, para las distintas opciones de su implementación; asimismo, se obtendrán vídeos del desarrollo (simulado) de la producción, que permitirán observar, de forma visual, la ejecución de los procesos.
El uso de la herramienta de simulación, permitirá comprobar cada una de las opciones a implementar y una mejor comprensión del sistema a estudiar. La simulación será especialmente indicada para procesos con un elevado número de recursos (trabajadores, máquinas, mesas de trabajo, grúas y elementos de transporte y mantención, etc.) que deberán ser compartidos.
Asimismo, la simulación estará indicada cuando el número de productos y/o referencias sea elevado y compartan los mismos recursos y espacios.
Fase 7. Fase de puesta en marcha: introducción por medio de reuniones de trabajo:
La nueva implementación se someterá fase a fase mediante grupos de trabajo, del equipo de proyecto con los responsables de las áreas involucradas de la empresa.
En cada reunión este grupo se planteará la propuesta derivada del estudio anterior para una fase de la implementación, se expondrá y se debatirá en grupo, para acordar la forma en que se llevará a cabo la implementación definitiva.
Finalmente, y sin apartarse de los principios lean, se propone validar el nuevo proceso mejorado con herramientas de simulación.
Llegados a este punto, vamos a ver un interesante vídeo:
Herramientas Lean.
Con el objetivo de alcanzar el cumplimiento de los principios de Lean Manufacturing se han desarrollado diferentes herramientas Lean orientadas a identificar, corregir y optimizar el proceso de producción, entre las más conocidas se encuentran:
- Las 5 S’s
- Just in Time (Justo a Tiempo)
- Cambio rápido de molde (SMED)
- Control autónomo de los defectos : Jidoka
- Control visual (Sistema Andon)
- Dispositivos para prevenir errores : Poka Yoke
- Kaizen (Mejora continua).
- Sistema Kanban.
- Estandarización de las operaciones.
- Mantenimiento productivo total (TPM).
- Mapa de la Cadena de valor (VSM).
El sistema de producción Toyota (TPS) se representa mediante una casa en la que se debe construir desde sus cimientos. Se ha venido utilizando no solo para visualizar algunas de las herramientas para su aplicación, sino también la filosofía que se encierra detrás de ella.
Para acabar, os dejo una muy interesante presentación titulada "Cómo convertir su empresa en una organización Lean".
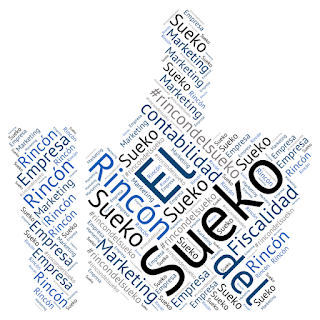
#rincondelsueko en Twitter, Facebook, Flipboard y Google+
No hay comentarios:
Publicar un comentario