
Como ya sabemo, el Lean Manufacturing se materializa en la práctica a través de la aplicación de una amplia variedad de técnicas, muy diferentes entre sí, que se han ido implementado con éxito en empresas de muy diferentes sectores y tamaños. Hoy hablaremos de una de esas técnicas: el SMED.
Ante todo, y con la intención de ser lo más didáctico posible, vamos a dar un primera definición de esta herramienta:
SMED por sus siglas en inglés (Single-Minute Exchange of Dies), es una metodología o conjunto de técnicas que persiguen la reducción de los tiempos de preparación de máquina. Esta se logra estudiando detalladamente el proceso e incorporando cambios radicales en la máquina, utillaje, herramientas e incluso el propio producto, que disminuyan tiempos de preparación.Estos cambios implican la eliminación de ajustes y estandarización de operaciones a través de la instalación de nuevos mecanismos de alimentación/retirada/ajuste/centrado rápido como plantillas y anclajes funcionales.
Es una metodología clara, fácil de aplicar y que consigue resultados rápidos y positivos, generalmente con poca inversión aunque requiere método y constancia en el propósito. La reducción en los tiempos de preparación merece especial consideración y es importante por varios motivos. Cuando el tiempo de cambio es alto los lotes de producción son grandes y, por tanto, la inversión en inventario es elevada. Cuando el tiempo de cambio es insignificante se puede producir diariamente la cantidad necesaria eliminando casi totalmente la necesidad de invertir en inventarios.
Los métodos rápidos y simples de cambio eliminan la posibilidad de errores en los ajustes de técnicas y útiles. Los nuevos métodos de cambio reducen sustancialmente los defectos y suprimen la necesidad de inspecciones. Con cambios rápidos se puede aumentar la capacidad de la máquina. Si las máquinas se encuentran a plena capacidad, una opción para aumentarla, sin comprar máquinas nuevas, es reducir su tiempo de cambio y preparación.
Cabe destacar que en las empresas japonesas la reducción de tiempos de preparación no sólo recae en el personal de producción e ingeniería, sino también en los Círculos de Control de Calidad (CCC). Precisamente, SMED hace uso de las técnicas de calidad para resolución de problemas como el análisis de Pareto, las seis preguntas clásicas ¿Qué? – ¿Cómo? – ¿Dónde? – ¿Quién? – ¿Cuándo? y los respectivos ¿Por qué?
Todas estas técnicas se usan a los efectos de detectar posibilidades de cambio, simplificación o eliminación de tareas de preparación a partir de identificar la causa raíz que determinan tiempos elevados de preparación o cambio de técnicas. En este sentido conviene tener presente las posibles causas que originan elevados de cambio:
- La terminación de la preparación es incierta.
- No se ha estandarizado el procedimiento de preparación.
- Utilización de equipos inadecuados.
- No haber aplicado la mejora a las actividades de preparación.
- Los materiales, las técnicas y las plantillas no están dispuestos antes del comienzo de las operaciones de preparación.
- Las actividades de acoplamiento y separación duran demasiado.
- Número de operaciones de ajuste elevado.
- Las actividades de preparación no han sido adecuadamente evaluadas.
- Variaciones en los tiempos de preparación de las máquinas.
Para llevar a cabo una acción SMED, las empresas deben acometer estudios de tiempos y movimientos relacionados específicamente con las actividades de preparación. Estos estudios suelen encuadrarse en cuatro fases bien diferenciadas:
Fase 1: Diferenciación de la preparación externa y la interna.
Por preparación interna, se entienden todas aquellas actividades que para poder efectuarlas requiere que la máquina se detenga. En tanto que la preparación externa se refiere a las actividades que pueden llevarse a cabo mientras la máquina funciona. El principal objetivo de esta fase es separar la preparación interna de la preparación externa, y convertir cuanto sea posible de la preparación interna en preparación externa. Para convertir la preparación interna en preparación externa y reducir el tiempo de esta última, son esenciales los puntos siguientes:
- Preparar previamente todos los elementos: plantillas, técnicas, troqueles y materiales...
- Realizar el mayor número de reglajes externamente.
- Mantener los elementos en buenas condiciones de funcionamiento.
- Crear tablas de las operaciones para la preparación externa.
- Utilizar tecnologías que ayuden a la puesta a punto de los procesos.
- Mantener el buen orden y limpieza en la zona de almacenamiento de los elementos principales y auxiliares (5S).
Fase 2: Reducir el tiempo de preparación interna mediante la mejora de las operaciones.
Las preparaciones internas que no puedan convertirse en externas deben ser objeto de mejora y control continuo. A tales efectos se consideran clave para la mejora continua de las mismas los siguientes puntos:
- Estudiar las necesidades de personal para cada operación.
- Estudiar la necesidad de cada operación.
- Reducir los reglajes de la máquina.
- Facilitar la introducción de los parámetros de proceso.
- Establecer un estándar de registro de datos de proceso.
- Reducir la necesidad de comprobar la calidad del producto.
Fase 3: Reducir el tiempo de preparación interna mediante la mejora del equipo.
Todas las medidas tomadas a los efectos de reducir los tiempos de preparación se han
referido hasta ahora a las operaciones o actividades. La siguiente fase debe enfocarse
a la mejora del equipo:
- Organizar las preparaciones externas y modificar el equipo de forma tal que puedan seleccionarse distintas preparaciones de forma asistida.
- Modificar la estructura del equipo o diseñar técnicas que permitan una reducción de la preparación y de la puesta en marcha.
- Incorporar a las máquinas dispositivos que permitan fijar la altura o la posición de elementos como troqueles o plantillas mediante el uso de sistemas automáticos.
Fase 4: Preparación Cero.
El tiempo ideal de preparación es cero por lo que el objetivo final debe ser plantearse la utilización de tecnologías adecuadas y el diseño de dispositivos flexibles para productos pertenecientes a la misma familia. Los beneficios de la aplicación de las técnicas SMED se traducen en una mayor capacidad de respuesta rápida a los cambios en la demanda (mayor flexibilidad de la línea), permitiendo la aplicación posterior de los principios y técnicas Lean como el flujo pieza a pieza, la producción mezclada o la producción nivelada.
Para acabar un vídeo de la UPV, que nos presenta una descripción de la herramienta SMED, de los objetivos conseguidos con su implementación y los pasos de los que consta dicha herramienta. Autor: Julio JuanGarcía Sabater.
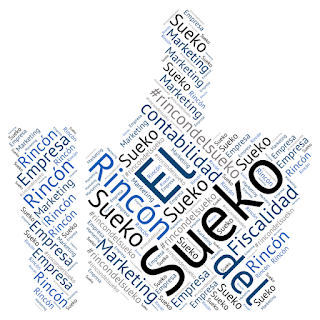
#rincondelsueko en Twitter, Facebook, Flipboard y Google+
No hay comentarios:
Publicar un comentario